GE Renewable Energy introduces wind turbine blade inspection technology
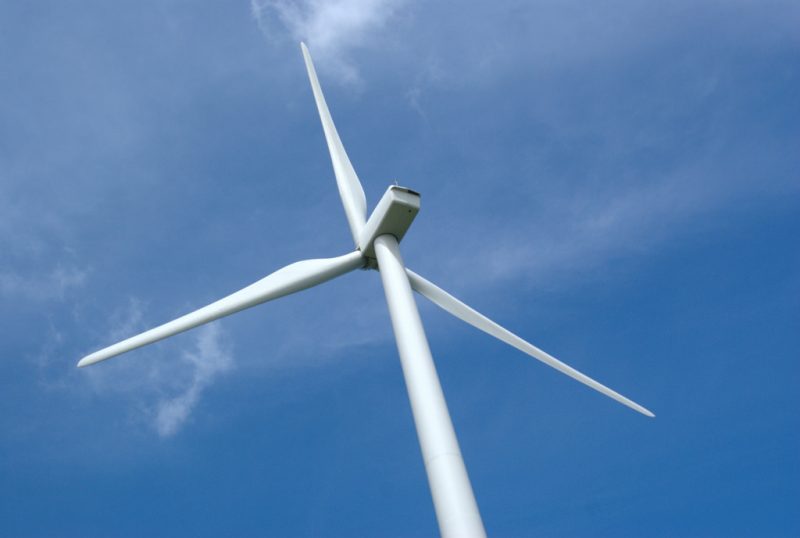
GE Renewable Energy launched a new ground-based blade inspection system that will reduce wind turbine blade operations and maintenance costs by up to 25 percent.
The blade inspection system combines thermal imaging technology and wide-band acoustic spectral analysis to detect anomalies on blades across an entire wind fleet. The patented system provides real-time data analytics on turbine health. This eliminates the need for inspections on the tower, making it safer and more effective. Also, users do not have to power down the wind turbines top do the inspections. Some 1500 turbines have been inspected using this technology to date. The inspection time is about 15 minutes per unit.
The inspection technology is placed at the base of a wind turbine. It takes a series of recordings of the blades as they are turning and under active load. It shows a real-time view of the subsurface health of a blade, layered with digital analytic capabilities that detect a wide range of anomalies. The inspection system can detect cracks, fiber waves, delamination, bonding issues, breaking or missing adhesive joints, splits, and defective repairs. Using artificial intelligence algorithms and the expertise of technicians, an in-depth analysis of the health of the blades can then be conducted.
“Wind turbine blade inspections have come a long way. Ground scopes, drones, and tap testing are just a few of the methods that operators have used to help prevent against failures both small and catastrophic,” Anne McEntee, CEO of Digital Services at GE Renewable Energy, said. “But most down-tower blade inspections are limited to showing what’s happening with the surface of a blade. Many of the issues that lead to larger failures are deeper within the blade itself. This is where our inspection technology truly excels. The ability to also look beyond the exterior coating of the blade, regardless of manufacturer, marks a significant advance in blade inspection technology for the entire wind industry.”